What Your Building's Cracks Are Telling You: Understanding Sealant Failure Signals
Key Takeaways
- Early Detection Saves Money: Identifying sealant failure early can prevent water damage that costs 5-10 times more to repair than simple sealant replacement.
- Different Cracks Mean Different Problems: Various crack patterns indicate specific issues—hairline cracks often signal normal aging while step cracks may indicate structural movement.
- Planned Maintenance Works: A proactive sealant inspection and replacement program typically costs 70% less than emergency repairs and prevents business disruption.
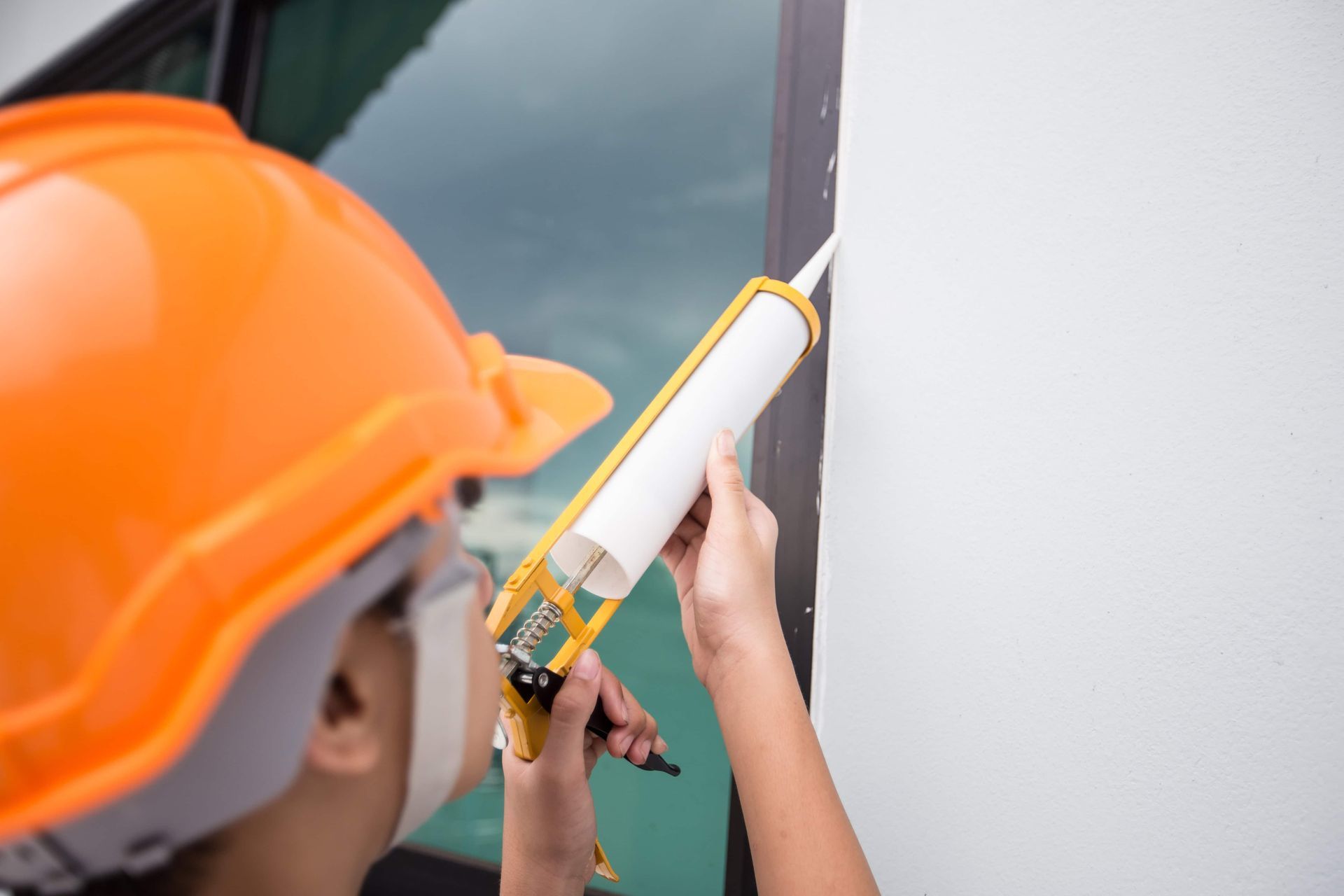
Those small cracks around your windows, doors, and building joints might not seem like a big deal. They're easy to overlook during your busy day managing a commercial property. But these seemingly minor imperfections are actually sending you important messages about your building's health—and ignoring them could be a costly mistake.
Sealants are your building's first line of defense against water, air infiltration, energy loss, and even structural damage. When they start to fail, they give specific warning signs that smart property managers learn to recognize and address before small problems become major expenses.
Why Building Sealants Matter
Before diving into failure signals, let's understand why sealants are so critical to your commercial building's performance:
The Water Barrier
Water is your building's worst enemy. Just one small breach in your sealant system can allow moisture to penetrate and cause:
- Rotting wood and deteriorating building materials
- Mold and mildew growth (with associated health concerns)
- Rust and corrosion of metal components
- Insulation damage and reduced R-value
- Interior water damage to finishes and contents
A single water intrusion event can cost thousands to repair—often 5-10 times more than preventative sealant maintenance would have cost.
The Energy Envelope
Failing sealants create gaps that compromise your building's energy efficiency:
- Air leakage can increase heating and cooling costs by 15-30%
- Temperature fluctuations create uncomfortable conditions for occupants
- HVAC systems work harder and wear out faster
- Utility bills climb steadily higher
Many property managers are shocked to discover how much they can save on energy costs simply by maintaining proper sealants.
Structural Movement Accommodation
Buildings aren't static—they're constantly moving in response to:
- Temperature fluctuations (thermal expansion and contraction)
- Wind loads
- Settlement
- Vibration
- Seismic activity
Sealants provide the flexibility to accommodate this movement without damage. When they fail, the building loses this crucial ability to flex and adapt.
Common Sealant Failure Signals and What They Mean
Now let's decode the specific messages your building is sending when sealants begin to fail:
1. Adhesive Failure
What it looks like: The sealant separates cleanly from one or both substrates (the materials it's supposed to connect), often peeling away like a strip.
What it's telling you: This usually indicates:
- Improper surface preparation before application
- Using the wrong sealant for your surfaces
- Movement beyond the sealant's capability
- Surface contamination during installation
Severity level: Moderate to high—these areas are already allowing water entry.
2. Cohesive Failure
What it looks like: The sealant itself splits or tears down the middle, with material still adhered to both sides of the joint.
What it's telling you: This typically means:
- Joint movement exceeded the sealant's capacity
- Improper joint design (wrong width-to-depth ratio)
- Aged sealant that has lost elasticity
- Exposure to chemicals that degraded the material
Severity level: High—these failures create direct pathways for water.
3. Surface Crazing/Cracking
What it looks like: A network of fine, shallow cracks on the sealant surface, similar to a dried mud pattern.
What it's telling you: This often indicates:
- UV degradation
- Natural aging
- Improper mixing of multi-component sealants
- Environmental stress
Severity level: Low to moderate initially, but will progress to more serious failure if not addressed.
4. Bubbling or Blistering
What it looks like: Small bubbles or raised blisters in the sealant surface.
What it's telling you: This is typically caused by:
- Moisture or solvent trapped within the sealant
- Application during high humidity or on damp surfaces
- Chemical incompatibility with adjacent materials
- Air entrapment during application
Severity level: Moderate—these bubbles can break open and create water entry points.
5. Chalking and Discoloration
What it looks like: Powdery residue on the surface or noticeable color change from the original application.
What it's telling you: This usually signals:
- UV degradation
- Chemical exposure
- Natural aging
- Poor quality sealant
Severity level: Low initially, but indicates the sealant is deteriorating and will soon fail functionally.
6. Hardening and Brittleness
What it looks like: Sealant becomes stiff, loses flexibility, and may have small pieces breaking off.
What it's telling you: This indicates:
- End of useful life
- Significant age degradation
- Inappropriate sealant selection
- Environmental stress
Severity level: High—brittle sealant cannot accommodate building movement and will continue to fail.
Where to Look: Critical Inspection Points
Knowing what to look for is just half the battle—you also need to know where to look. These areas deserve special attention during sealant inspections:
Building Exterior Joints
- Expansion joints: Look for compression failures or extrusion
- Control joints: Check for separation and movement
- Perimeter joints: Examine where different materials meet
Window and Door Systems
- Window perimeters: Check for separation from surrounding materials
- Mullions and transitions: Look for gaps and failures
- Door thresholds: Examine for wear and separation
Roof-Wall Intersections
- Parapet caps: Inspect for splits and separations
- Termination bars: Check for pulling away from surfaces
- Flashing transitions: Look for gaps and openings
Penetrations
- Vents and pipes: Examine sealant around all penetrations
- Electrical and mechanical entries: Check for gaps and deterioration
- Signage attachments: Look for water entry points around fasteners
Wet Areas
- Around plumbing fixtures: Check for water damage signs
- Exterior water features: Examine for leakage and deterioration
- Drainage systems: Look for separation around drains and scuppers
The Weather Factor: Environmental Impacts on Sealant Performance
Your building's location and climate significantly affect how sealants perform and fail:
High-Temperature Regions
In hot climates, watch for:
- Accelerated UV degradation and surface crazing
- Faster aging and hardening
- More pronounced expansion and contraction cycles
Buildings in Southeast Pennsylvania experience hot summers that can take a toll on sealants, especially on south and west-facing exposures.
Cold-Weather Effects
During cold periods, be alert for:
- Reduced flexibility and increased brittleness
- Contraction that may exceed sealant capacity
- Freeze-thaw damage when moisture penetrates cracks
Our Pennsylvania winters create significant thermal stress on building sealants, making regular inspection crucial.
Rain and Moisture Exposure
Areas with high rainfall require attention to:
- Signs of water infiltration (staining, efflorescence)
- Biological growth (algae, mold) indicating moisture presence
- Sealant washout in improperly protected areas
Industrial Environments
Buildings near industrial areas should check for:
- Chemical degradation from air pollutants
- Accelerated aging from environmental stress
- Discoloration indicating chemical attack
From Recognition to Action: Addressing Sealant Failures
Once you've identified sealant problems, what's the next step? Here's a practical approach:
1. Assess the Scope
Determine if you're dealing with:
- Isolated failures (spot repairs may suffice)
- Systematic failures (more comprehensive approach needed)
- Age-related deterioration (full replacement may be most cost-effective)
2. Identify the Root Cause
Work with professionals to determine why the failure occurred:
- Was it a product failure?
- An application issue?
- A design problem?
- Normal aging?
Understanding the cause prevents repeating the same mistakes.
3. Develop the Right Solution
Based on the assessment, create a plan that might include:
- Spot repairs for isolated issues
- Partial replacement of the most critical areas
- Complete system replacement
- Redesign of problematic joints
4. Proper Preparation is Everything
The most common reason sealant repairs fail is inadequate preparation:
- Complete removal of old sealant
- Thorough cleaning of substrates
- Proper priming when required
- Attention to moisture content and temperature
Skipping these steps virtually guarantees premature failure of the new application.
5. Select the Right Product
Not all sealants are created equal. Selection should consider:
- Joint movement requirements
- Substrate compatibility
- UV and weather exposure
- Expected service life
- Aesthetic requirements
A professional commercial sealant contractor like PR Commercial Painting can help guide this critical decision.
Preventative Approach: The Maintenance Advantage
The smartest way to handle sealant failures is to prevent them in the first place. A planned maintenance program typically includes:
Regular Inspection Cycles
- Annual comprehensive inspections
- Additional checks after extreme weather events
- Documentation of developing issues
- Photographic records to track changes over time
Timely Intervention
- Addressing minor issues before they become major ones
- Strategic scheduling during favorable weather conditions
- Coordination with other building maintenance activities
- Budgeting for planned rather than emergency expenses
System Documentation
- Keeping records of sealant types and locations
- Tracking installation dates and expected service life
- Documenting previous repairs and their effectiveness
- Building a maintenance history that informs future decisions
The Cost of Waiting: Why Prompt Response Matters
Delaying sealant repairs carries significant financial risk:
The Multiplication Effect
What begins as a simple sealant replacement can quickly escalate:
- A $5,000 sealant job left unaddressed for too long can trigger $25,000-$50,000 in water damage repairs
- Structural damage from ongoing water intrusion can push costs into six figures
- Business interruption during emergency repairs adds indirect costs
The Hidden Damage Timeline
Water damage doesn't announce itself immediately:
- Moisture can penetrate for months or years before interior damage becomes visible
- By the time you see water stains, significant damage has already occurred
- Mold can develop within 24-48 hours of water intrusion but may remain hidden inside walls
Energy Loss Costs
Failed sealants create ongoing expenses through:
- Increased heating and cooling costs
- Greater HVAC wear and tear
- Uncomfortable conditions that affect occupant productivity
Conclusion: Listen to What Your Building is Telling You
Your building communicates through its condition—and those small cracks and failures are important messages about its health and needs. Learning to recognize these signals allows you to respond proactively, preventing minor issues from becoming major expenses.
Regular inspection, timely maintenance, and appropriate repairs of your commercial building's sealants represent one of the most cost-effective ways to protect your investment. The return on a well-planned sealant maintenance program typically exceeds 500% when considering avoided repair costs, energy savings, and extended building component life.
For commercial property owners in Southeast Pennsylvania, PR Commercial Painting offers comprehensive sealant inspection, maintenance, and repair services. Our experienced teams understand the unique challenges of commercial buildings and provide solutions focused on long-term protection and value.
PR Commercial Painting provides professional commercial caulking and sealing services throughout Southeast Pennsylvania, South Jersey, and North Delaware. Contact us today at 610-232-7332 to schedule a sealant assessment or discuss a maintenance program for your commercial property.
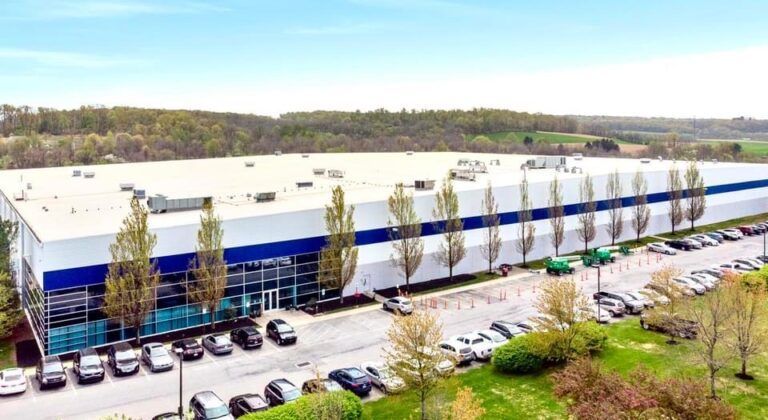
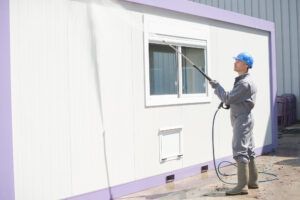
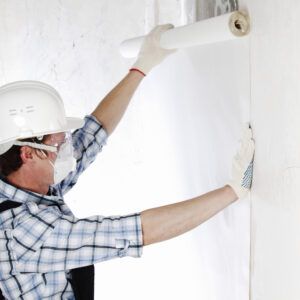
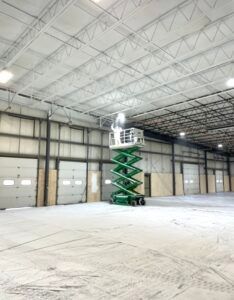