Beyond Bare Concrete: Choosing the Right Floor Coating System for Your Commercial Facility
Key Takeaways
- Performance Matching: Different commercial environments require specific floor coating properties—matching your facility's exact needs can extend floor life by 5-10 years.
- Safety Benefits: Properly selected floor coatings reduce slip-and-fall incidents by up to 80% while improving visibility and reducing maintenance costs.
- Long-Term Value: While quality commercial floor coatings represent a higher initial investment, they typically reduce lifetime flooring costs by 40-60% compared to untreated concrete or budget solutions.
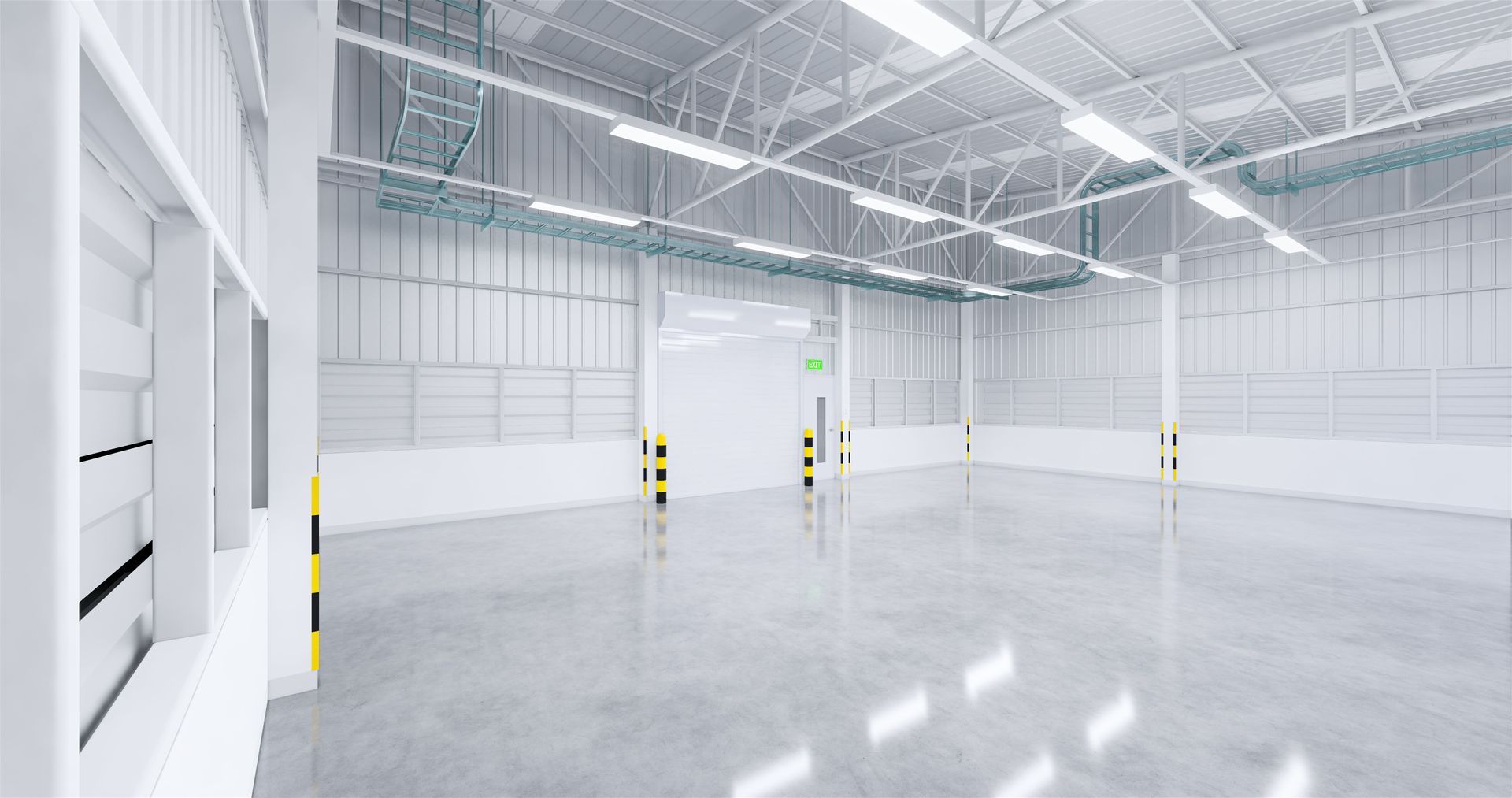
Walk into any commercial facility with bare concrete floors, and you're looking at a missed opportunity. Uncoated concrete isn't just aesthetically underwhelming—it's porous, prone to dusting, difficult to clean, and offers minimal protection against chemicals, impacts, and wear.
Modern commercial floor coating systems transform this basic building material into high-performance surfaces tailored to your specific operational needs. But with so many options available, how do you choose the right system for your facility?
Why Bare Concrete Falls Short
Before exploring coating options, it's worth understanding why uncoated concrete rarely meets commercial needs:
The Porosity Problem
Concrete might look solid, but it's actually quite porous. This porosity allows:
- Liquids to penetrate and stain
- Bacteria and contaminants to embed
- Oils and chemicals to soak in
- Moisture to migrate upward from the substrate
Even the best cleaning methods can't fully remove contaminants once they've penetrated concrete's porous surface.
Durability Limitations
Untreated concrete is vulnerable to:
- Surface abrasion and wear patterns
- Dusting (the release of fine concrete particles)
- Chemical attack from even mild substances
- Freeze-thaw damage in exterior applications
- Cracking from impact and point loads
Maintenance Challenges
Maintaining bare concrete requires:
- More frequent cleaning
- Stronger chemicals
- More labor-intensive methods
- Regular dust control measures
- Periodic resurfacing
These limitations explain why most commercial and industrial facilities eventually coat their concrete floors. The question isn't whether to coat, but which system will deliver the best performance for your specific needs.
Understanding Commercial Floor Coating Systems
Let's explore the major coating categories and their ideal applications:
Epoxy Floor Coatings
What they are: Thermosetting resins that cure to form a hard, durable surface when mixed with a hardener.
Best for:
- General commercial and industrial use
- Moderate chemical exposure
- High-traffic areas
- Environments where durability is prioritized over flexibility
Strengths:
- Excellent adhesion to properly prepared concrete
- Outstanding chemical resistance
- Good abrasion resistance
- Variety of finish options (smooth, non-slip, decorative)
- Self-leveling properties for flat, even surfaces
- Cost-effective for large areas
Limitations:
- Can yellow when exposed to UV light
- Limited flexibility once cured
- Temperature sensitivity during application
- Longer cure times than some alternatives
Typical applications:
- Warehouses and distribution centers
- Manufacturing floors
- Commercial garages
- Retail spaces
- Healthcare facilities
- Food processing (with specialized formulations)
Polyurethane Floor Coatings
What they are: Polymer-based coatings that offer greater flexibility and abrasion resistance than epoxies.
Best for:
- Areas with temperature fluctuations
- Spaces requiring higher impact resistance
- Environments with moderate to heavy traffic
- Applications needing UV stability
Strengths:
- Superior abrasion resistance
- Better flexibility than epoxy
- Excellent impact resistance
- Good chemical resistance
- UV stable (minimal yellowing)
- Faster curing than many epoxies
Limitations:
- Higher cost than basic epoxy systems
- May require an epoxy primer for best adhesion
- Less chemical resistance than some specialized epoxies
- More sensitive to moisture during application
Typical applications:
- Loading docks
- Manufacturing with heavy equipment
- Cold storage facilities
- Exterior walkways and patios
- High-traffic retail
- Sports facilities
Polyaspartic Coatings
What they are: Advanced aliphatic polyurea coatings that offer rapid curing and excellent durability.
Best for:
- Projects requiring minimal downtime
- Areas needing same-day return to service
- Applications demanding both durability and aesthetics
- Wide temperature range installations
Strengths:
- Extremely fast cure times (hours versus days)
- Excellent UV stability
- Superior chemical resistance
- Great abrasion resistance
- Wide temperature application range
- Low to zero VOCs
Limitations:
- Higher cost than conventional systems
- Requires skilled installation due to fast cure time
- Less flexible than polyurethane
- May be slippery without proper additives
Typical applications:
- Retail floors requiring minimal business interruption
- Car showrooms
- Restaurants and commercial kitchens
- Healthcare facilities
- Locations requiring winter installation
- Garages and auto service centers
Methyl Methacrylate (MMA) Coatings
What they are: Acrylic-based resins that cure extremely quickly, even at very low temperatures.
Best for:
- Projects requiring the absolute minimum downtime
- Cold weather applications
- Food processing with strict sanitation requirements
- Environments with extreme temperature variations
Strengths:
- Incredibly fast cure (1-2 hours to full service)
- Can be applied in subfreezing temperatures
- Excellent chemical resistance
- Good wear resistance
- Seamless, sanitary finish
- Can bond to existing coatings
Limitations:
- Strong odor during installation
- Higher cost than conventional systems
- Requires specialized application equipment
- Flammable during application
Typical applications:
- Food and beverage processing
- Cold storage and freezers
- Commercial kitchens
- Pharmaceutical facilities
- 24/7 operations requiring minimal shutdown
- Winter construction projects
Specialized Coating Systems
Beyond these major categories, several specialized systems address specific needs:
Antimicrobial Flooring
- Incorporates biocides to inhibit bacterial growth
- Ideal for healthcare, food processing, and laboratories
- Often combined with epoxy or urethane base systems
ESD (Electrostatic Discharge) Flooring
- Controls static electricity in sensitive environments
- Critical for electronics manufacturing
- Protects against equipment damage and ignition hazards
Thermal Shock Resistant Systems
- Withstands extreme temperature changes
- Essential for food processing with hot water washdowns
- Often utilizes urethane cement technology
Chemical-Resistant Novolac Epoxies
- Provides superior resistance to harsh chemicals
- Used in battery charging areas, chemical processing
- Offers protection against acids, caustics, and solvents
Matching Your Facility's Needs to the Right System
Selecting the optimal floor coating involves assessing several key factors:
Traffic Patterns and Load Types
Consider:
- Foot traffic volume and patterns
- Wheeled traffic (forklifts, pallet jacks, carts)
- Static loads (equipment, storage)
- Impact frequency and intensity
Higher traffic areas typically benefit from polyurethane or polyaspartic topcoats over epoxy base layers for maximum durability.
Chemical Exposure
Identify all chemicals your floor might encounter:
- Cleaning solutions
- Process chemicals
- Food acids
- Oils and lubricants
- Salts and de-icing compounds
For harsh chemical environments, specialized epoxy systems like novolac formulations offer superior protection.
Cleaning Requirements
Your cleaning protocol affects coating selection:
- Hot water cleaning requires thermal shock resistance
- Steam cleaning demands specialized systems
- Frequent sanitizing may require antimicrobial properties
- Harsh cleaning chemicals need compatible coatings
Downtime Tolerance
How quickly must the floor return to service?
- Standard epoxies: 5-7 days before full service
- Polyurethanes: 3-5 days
- Polyaspartics: 1-2 days
- MMA systems: Same day (2-4 hours)
Faster-curing systems typically cost more but may save significantly in reduced operational disruption.
Aesthetic Requirements
Consider the visual impact:
- Solid colors vs. decorative systems
- High-gloss vs. satin or matte finishes
- Incorporation of company colors or logos
- Demarcation of zones and traffic paths
Many modern systems combine performance with outstanding aesthetics, eliminating the need to choose between function and appearance.
Safety Considerations
Floor coatings can enhance workplace safety through:
- Slip resistance additives
- Light-reflective properties
- Clear demarcation of hazards and pathways
- Elimination of trip hazards from damaged concrete
Environmental Factors
Consider:
- Moisture issues in the concrete
- Temperature fluctuations
- UV exposure
- Humidity conditions
- Indoor air quality requirements
These environmental conditions can significantly impact which coating system will perform best in your facility.
Popular Commercial Floor Coating Systems by Industry
Different industries typically have specific requirements that guide coating selection:
Manufacturing and Industrial
Common choice: Hybrid systems with epoxy base coats and polyurethane topcoats
Why it works: This combination provides chemical resistance from the epoxy with added abrasion resistance from the urethane topcoat—ideal for the diverse demands of industrial environments.
Enhancement options:
- Line striping for workflow organization
- Custom colors for zone identification
- Anti-static properties for sensitive areas
- Varying degrees of slip resistance
Food and Beverage Processing
Common choice: Urethane cement systems or MMA coatings
Why it works: These systems withstand thermal shock from hot water cleaning, provide antimicrobial protection, and resist food acids and sanitizing chemicals.
Enhancement options:
- Integral cove base for seamless wall-to-floor transitions
- Specialized textures for wet processing areas
- Rapid cure formulations for minimal downtime
- USDA/FDA compliant formulations
Healthcare Facilities
Common choice: Seamless epoxy or polyaspartic systems
Why it works: These provide easy-to-clean, antimicrobial surfaces with excellent chemical resistance to disinfectants and stain resistance to bodily fluids.
Enhancement options:
- Low-VOC or zero-VOC formulations
- Decorative flake or quartz for aesthetics and slip resistance
- Custom colors for wayfinding or department identification
- UV-cured systems for minimal odor
Retail and Commercial Spaces
Common choice: Decorative epoxy or polyaspartic systems
Why it works: These systems combine durability with aesthetic appeal, standing up to high foot traffic while enhancing the customer experience.
Enhancement options:
- Metallic epoxy finishes for dramatic visual impact
- Embedded logos or designs
- High-gloss finishes for light reflection
- Quick-cure options for overnight installation
Warehousing and Distribution
Common choice: High-build epoxy with polyurethane topcoat
Why it works: This system provides excellent durability against forklift traffic and pallet dragging while resisting damage from dropped items.
Enhancement options:
- Line striping for organization
- ESD properties for electronic storage
- High-reflectivity for improved lighting efficiency
- Varying textures for different functional areas
The Installation Process: What to Expect
Understanding the installation process helps you plan effectively and ensures quality results:
1. Surface Preparation
The most critical step in any floor coating project is proper surface preparation:
- Mechanical preparation (shot blasting, diamond grinding)
- Crack and joint treatment
- Moisture testing and mitigation if needed
- Concrete profiling to create the proper anchor pattern
This step typically represents 60-70% of the labor in a quality installation.
2. Primer Application
Most systems begin with a primer coat that:
- Penetrates and seals the concrete
- Improves adhesion of subsequent layers
- Addresses minor substrate issues
- Blocks moisture vapor transmission (specialized primers)
3. Base Coat Application
The main body of the system provides:
- Build thickness for durability
- Self-leveling properties to correct minor unevenness
- The primary protective layer
- The foundation for decorative elements if applicable
4. Broadcast Aggregates (Optional)
For slip resistance or decorative effects:
- Quartz sand for industrial non-slip texture
- Decorative quartz or vinyl flakes for appearance
- Aluminum oxide for extreme wear resistance
- Glass beads for moderate texture with cleanability
5. Topcoat Application
The final layer(s) provide:
- Sealing of broadcast materials
- Enhanced chemical and abrasion resistance
- The desired finish (gloss, satin, or matte)
- UV protection if needed
- The primary wear surface
6. Cure Time
Before returning the floor to service:
- Light foot traffic: 12-24 hours for most systems
- Heavy foot traffic: 24-48 hours
- Vehicle traffic: 3-7 days (system dependent)
- Chemical exposure: 5-7 days for full cure
- Water exposure: Varies by system
Accelerated systems can dramatically reduce these timeframes but may come with higher costs.
Investing Wisely: Cost Considerations
Floor coating costs vary widely based on:
System Type and Complexity
- Basic single-coat sealers: $2-4 per square foot
- Standard epoxy systems: $5-8 per square foot
- High-performance epoxy/urethane: $7-12 per square foot
- Decorative broadcast systems: $8-15 per square foot
- Specialized systems (MMA, urethane cement): $12-20+ per square foot
Life-Cycle Cost Analysis
When evaluating costs, consider the total life-cycle expense:
- Initial installation cost
- Expected service life before major maintenance
- Routine maintenance requirements and costs
- Operational impact of future replacement
- Performance benefits that affect other expenses
A higher initial investment often delivers significantly lower long-term costs. For example, a quality epoxy/urethane system might cost twice as much as a basic coating but last three to four times longer with better performance throughout its life.
Maintaining Your Commercial Floor Coating
Proper maintenance extends coating life and performance:
Daily Maintenance
- Sweep or dust mop to remove abrasive particles
- Clean spills promptly to prevent staining or damage
- Use proper dilution of manufacturer-recommended cleaners
Weekly/Monthly Maintenance
- Scrub with automatic scrubber or mop and approved cleaners
- Inspect for damages and address minor issues promptly
- Maintain proper drainage to prevent standing water
Annual Maintenance
- Perform detailed inspection for wear, damage, or failure
- Consider light scuff and recoat of topcoat in high-wear areas
- Address any joint or crack deterioration
What to Avoid
- Harsh chemicals not approved by the coating manufacturer
- Dragging heavy objects across the surface
- Using abrasive cleaning pads that can scratch the surface
- Allowing standing water or chemical puddles to remain
Common Floor Coating Failures and How to Avoid Them
Understanding potential failures helps ensure successful installations:
Delamination
Causes: Inadequate surface preparation, moisture issues, incompatible materials
Prevention: Proper concrete profiling, moisture testing, compatible primer systems
Bubbling and Blistering
Causes: Moisture vapor transmission, air entrapment, application in direct sunlight
Prevention: Moisture mitigation systems, proper application techniques, controlled environment
Cracking
Causes: Concrete movement, inflexible coating over active cracks, impact damage Prevention: Proper joint treatment, appropriate crack isolation, suitable coating flexibility
Premature Wear
Causes: Insufficient coating thickness, improper system selection, poor surface preparation Prevention: Application to manufacturer specifications, appropriate system for traffic conditions
Color Fading
Causes: UV exposure, chemical attack, improper cleaning
Prevention: UV-stable topcoats, appropriate chemical resistance, proper maintenance
Conclusion: Making the Right Choice for Your
Facility
Selecting the right commercial floor coating system represents a significant opportunity to improve your facility's performance, safety, and aesthetics. By understanding your specific operational needs and the capabilities of different coating technologies, you can make an informed decision that delivers long-term value.
The most successful projects begin with thorough assessment and planning. Consider partnering with an experienced commercial coating contractor like PR Commercial Painting who can evaluate your unique requirements and recommend appropriate solutions. With proper selection, installation, and maintenance, your coated concrete floor will deliver years of outstanding service while enhancing your facility's appearance and functionality.
For commercial facilities in Southeast Pennsylvania, PR Commercial Painting offers comprehensive floor coating services with an emphasis on durable, high-performance systems tailored to your specific needs. Our experienced teams understand the unique challenges of commercial environments and provide solutions focused on long-term value and performance.
PR Commercial Painting provides professional commercial floor coating services throughout Southeast Pennsylvania, South Jersey, and North Delaware. Contact us today at 610-232-7332 to discuss the ideal floor coating system for your commercial or industrial facility.
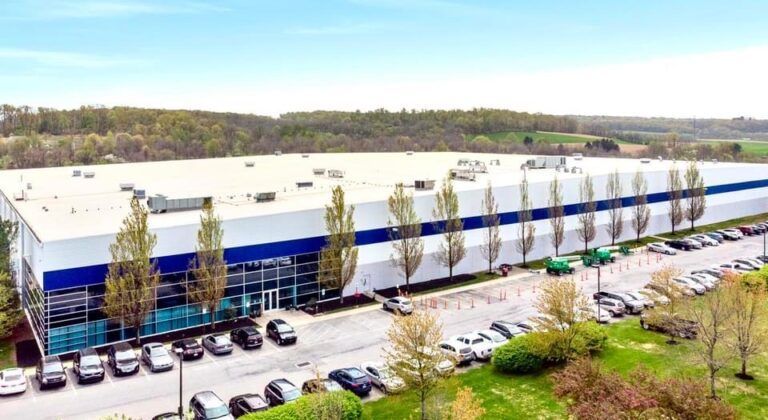
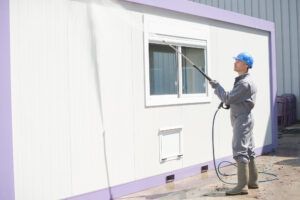
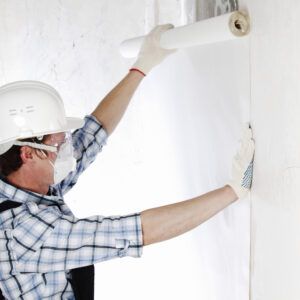
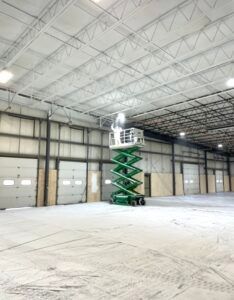